Battery Handling & Testing
Handling Lithium Thionyl Chloride Cells
Lithium cells are tremendous sources of electrochemical energy. As such, they are potentially dangerous if used or handled improperly. Great respect should be given to these cells. Several suggestions which deal with handling lithium cells in a safe and efficient manner follow.
Storage
Upon receipt cells should be left in the boxes they arrive in right until they are required for use. This will ensure that cells are separated from each other and the chance of an external short circuit occurring is significantly reduced.
Storage areas should be marked with appropriate signage indicating that lithium batteries are located in this area and no water fire extinguishers can be used if a fire occurs. Class D fire extinguishers or powder should be placed in the storage area and also be marked. The storage area should not be located near other flammable storage areas, water tanks, water supply, high humidity areas, or in locations where they may be easily flooded.
An additional safety precaution would include placing some baking soda powder near by and placing appropriate signage indicating that this is available. The baking soda is helpful should the cell vent or leak and electrolyte leak out as part of the effluent. The electrolyte is quite corrosive and can be neutralized by sodium phosphate.
Material Safety Data Sheets (MSDS) should also be placed in the storage area to provide personnel with information regarding the nature of the commodity being stored.
Ideal temperature range to store cells would be from 0 – 25 C. This will protect the shelf life of the cells and enhance their ability to perform when required. A well ventilated area is also helpful.
Handling
All contact with cells must be done with non-conductive materials. Any physical measuring required must be done with plastic calipers. Metal calipers may cause a short to be applied to the cell. Open circuit voltage (OCV) tests may be performed with standard voltmeters. Any type of load test can influence the future performance of the battery. It is best if Engineered Power is contacted before these tests are performed.
Additionally, any type of temperature, shock, or vibration testing performed on live cells should be approved by Engineered Power. We have the capacity to perform many of these tests in-house. If we cannot perform the test in-house, we have access to state of the art laboratory facilities to perform various testing at local academic and R&D institutions.
All work surfaces where the cells will be placed should consist of non-conductive materials. If cells are being configured into battery packs and the insulating shrink wrap, used to protect cell during shipping, must be removed, care must be taken to prevent the tab from the top of the cell coming into contact with the cell can. Racks or trays designed to prevent cells from contacting one another are recommended.
Tabs which extend from the top of the cell are attached to the cell below the visible surface. These tabs are made from thin metal materials and can break or tear if handled roughly.
Care should be taken to avoid heating of the cells during battery pack assembly. Soldering directly to the can/case is not recommended and should be avoided as it may cause localized overheating. Wave soldering processes and the exothermic property’s of some potting or encapsulant materials must be carefully evaluated prior to use. If there are any questions about an activity that you require to perform on a cell, please contact Engineered Power for assistance.
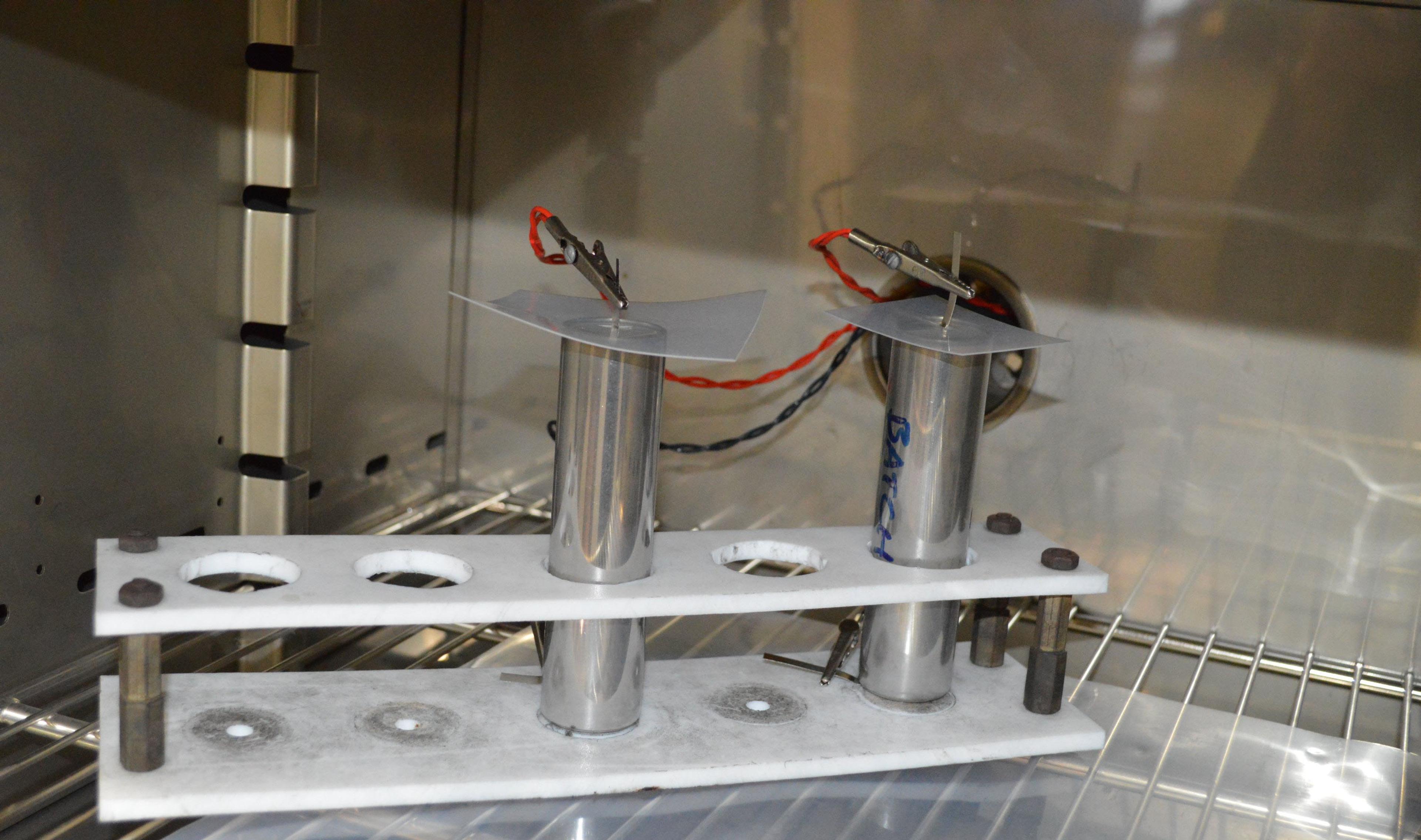
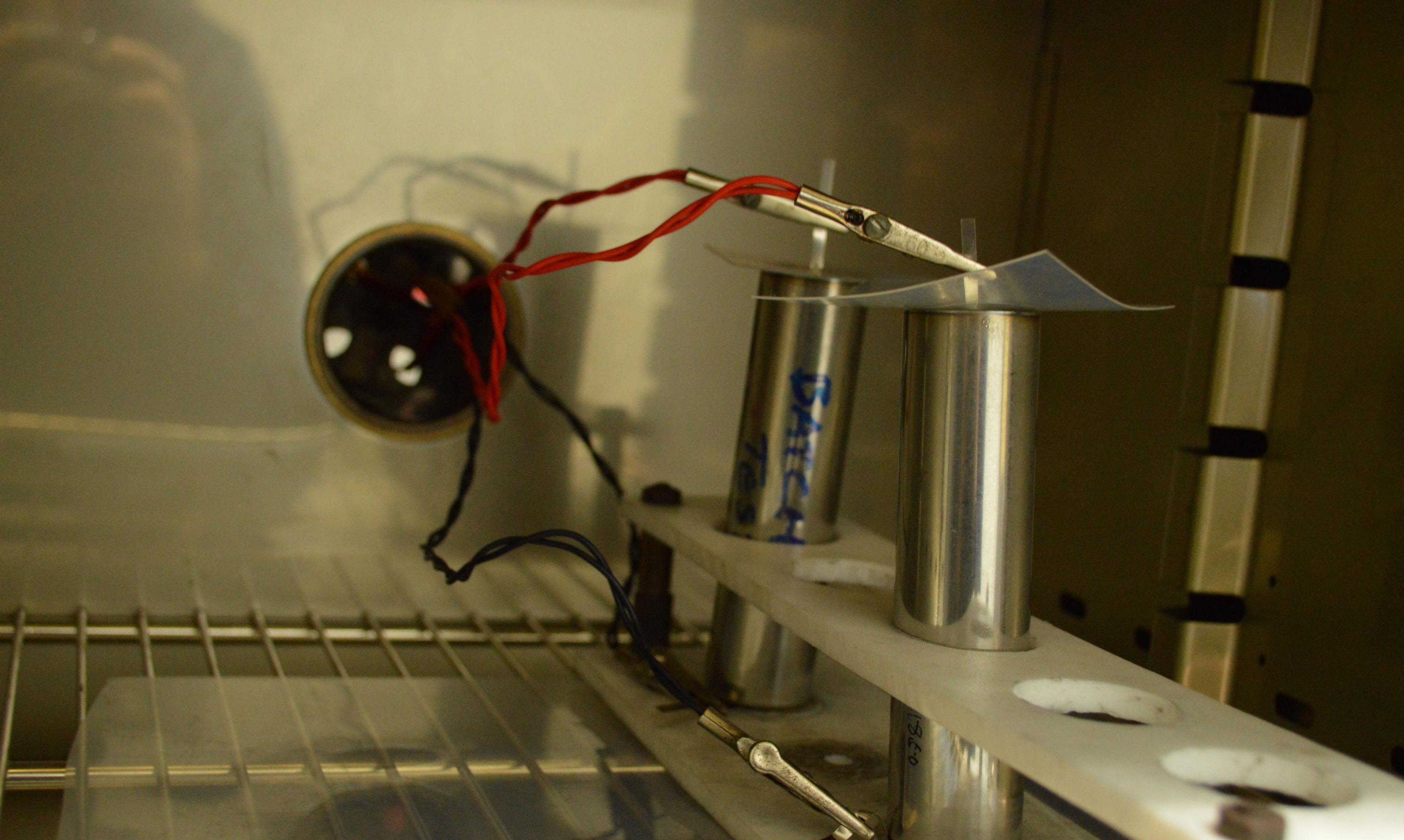
Testing
Engineered Power has a state of the art ARBIN cell testing unit. This equipment allows us to fully test the capacity of any cells we manufacture. Detailed records track the historical averages of capacity for every cell we make, and comparisons are done to ensure that the capacity is in line or better than specified in our cell rating sheets.
When coupled with an oven or environmental chamber this equipment can also be programmed to do specific tests at any temperature to create more empirical results as a part of the testing system. This allows us to run a test on your specific application before the cells go into service. The equipment allows us to test a cell down to a voltage of .1V per cell. Constant current range is between 1μA to 40A as well as pulse testing.
The maximum data logging rate is 2000 points per second with a 5ms minimum step time. Several different tests can be programmed into one testing schedule. For example, a continuous drain for a certain time period can be followed by pulses of varying currents and time durations.
Voltage, current, time, Amp-hours and Watt-hours are all parameters which can be tracked.